Crossing the Des Plaines River Shortcrossing Provides Big Challenges
When it comes to tunneling, the City of Joliet, Illinois, may not have the wealth of experience that some other, major urban centers may have. After all, there are no subways to dig, no mountains to traverse. But that doesn’t mean it can’t tackle a tricky project. Recently, the City successfully completed a bore under the Des Plaines River as part of its program to improve water quality.
The keys to success? Proper planning, assembling a strong team, and collaboration.
At first glance, the project looked fairly routine: build an 865-ft tunnel, 111.5 in. in diameter, underneath the Des Plains River. But there was one interesting wrinkle. Due to the fact that the river was channelized in the 1920s, the eastern shaft elevation was lower than the elevation of the river. That meant that if any water from the river found its way into the tunnel, there would be a potential for large-scale flooding.
Recognizing this potential, the City worked with the contractor, Triad/Midwest Mole IV, to develop a unique pilot bore approach to verify the ground conditions along the tunnel route, ensuring that tunneling could be constructed without risk of flooding. With peace of mind, the tunnel was then successfully bored, moving Joliet one step closer to improving water quality in the Des Plaines.
Project Background
The area that is now Joliet was first settled in the 1830s and was incorporated as a city in 1852. Like in many other eastem and Midwestern cities of the day, combined sewers — containing both sanitary and storm water flows — were built in the city’s core. The Des Plaines River Crossing is part of Phase II of Joliet’s 1ong-term control plan to capture excess storm water flow and convey it to a new wet weather treatment facility.
The new tunnel will convey excess flows from the westem side of the river to the eastern side, site of the existing treatment plant as well as the future wet weather facility. The City of Joliet worked with consulting firm Strand Associates in the development of the long-term control plan, which included the construction of the tunnel.
Once the tunnel project advanced to the design phase, Mott MacDonald was brought in to perform a risk analysis and was later retained as resident engineer in a joint venture with V3.
A joint venture of Triad/Midwest Mole was the tunneling subcontractor for the project and used a contractor—refurbished Lovat RM110 IBM with a Robbins Rockhead to mine the tunnel.
“While a tunnel of this length and diameter may not be considered big within the tunneling world, for us it was a significant undertaking,” said Allison Swisher, Civil Engineer, City of Joliet. “Not only was this our first tunnel, but the potential of flooding added a level of concern going into the project.”
GZA GeoEnvironmental conducted the geotechnical exploration, which included seven borings on both land and in water. The data showed competent rock at the design tunnel elevation below the river. With the rock conditions and short length of the tunnel, drill—and-blast was thought to be the most likely construction method. However, when the five bids were opened, the lowest – submitted by Joseph J. Henderson & Son – proposed TBM tunneling.
A joint venture of Triad/Midwest Mole was the tunneling subcontractor for the project and used a contractor—refurbished Lovat RM110 TBM with a Robbins Rockhead to mine the tunnel from west to east through dolostone bedrock with expected unconfined compressive strength of about 18,000 psi. The cutting diameter of the TBM was set at 111.5 in. Aldea Services was retained as the contractor’s designer.
Joseph J. Henderson & Son constructed the launch shaft while Triad/Midwest Mole constructed the reception shaft. Shaft construction involved drilling and blasting and the installation of ring beam and lagging in overburden and rock bolts in the bedrock.
The initial plans for tunneling included drilling probe holes in advance of the excavation, but the use of a small TBM with limited face access and room for extra equipment made this approach less practicable. So, Triad/Midwest Mole proposed drilling a 6-in. pilot hole adjacent to the tunnel alignment at the elevation of the tunnel crown. The contractor built an entry seal and gate valve on the shaft wall in the event that water was encountered. Using a Vermeer 100×120 horizontal directional drill, an Inrock hammer and Inrock guidance system, Triad/Midwest Mole completed the probe to the satisfaction of owner.
“We encountered an occasional clay seem during the bore, but very little groundwater,” said Steve Abernathy, Vice President, Midwest Mole. “The ground was very consistent with what they found in the boring. We got about 6-8 gpm of water coming out of the probe hole, which gave us a high degree of confidence that we weren’t going to encounter any catastrophic flows.”
As a contingency, the contractor was required to have dewatering pumps in the shafts capable of moving 2 gpm for every 10 ft of tunnel-equal to about 1,600 gpm over the length of the tunnel.
Navigating the probe drill also presented a challenge. The City had to coordinate with the Illinois Department of Transportation to set up tracking equipment on the I-80 bridge, as well as with the Department of Natural Resources to manage boat traffic that could also interfere with navigation.
“Completing the probe drill without encountering any major inflows helped put us at ease that we would not find a fissure or connection to the river while tunneling,” Swisher said. “We were pleased with the out-of-the-box way of addressing our concems.”
Moving Out
Once the probe was completed and the project team was comfortable with proceeding with TBM tunneling, Triad/Midwest Mole launched the machine. Because the TBM was configured for hard rock with grippers, the contractor affixed a steel tube to the bottom of the shaft in which the TBM was placed. The TBM then used its grippers to grip the inside of the pipe and push its way forward. As soon as the machine had entered the rock far enough, the steel starter tubes were removed.
“The shaft was going to be used for a pump station, so it was large enough to allow launching the machine this way,” said Brian Liotti, Project Engineer, Midwest Mole. “We were able to use this approach in lieu of building a starter tunnel by drill-and-blast.”
Once underway, crews were able to advance an average of about 20-30ft per day working 11-hour shifts. Tunneling began late July 2015 and was completed on Dec. 21. At the shallowest point along the alignment, there were 24 ft of cover.
Crew placed 60-in. diameter Hobas pipe to carry wet weather flows, in addition to two 24-in. sanitary sewer pipes and two 6-in. PVC conduits, which were grouted in place using 200 psi cellular grout.
First Time Owner’s Approach
Despite the relatively short length and small diameter, the Des Plaines River Crossing was a major undertaking for the City of Ioliet. As such, the City did its due diligence in preparing for the project, engaging consultants and the contracting community to utilize best practices and maximize its chances for success.
“The City did not have experience in tunneling, but understood that tunneling under a river and flood wall carried unique risks,” said Mike Vitale, Senior Vice President and Regional U.S. Tunnel Practice Leader at Mott MacDonald. “They were proactive in seeking out specialist tunneling advice from the onset of the project and receptive to implementing recommended risk mitigation measures. The City was a great client to work for.”
Joliet undertook a risk analysis, used a geotechnical baseline report(GBR) as part of the contract documents, and employed a dispute resolution board. As it turned out, the DRB was not needed “but was a good backstop,” according to Swisher.
“The most critical element in completing this tunnel was that we were able to get the right project team involved early on,” Swisher said. “Once the team was in place, we maintained communication and everyone was able to work well together.”
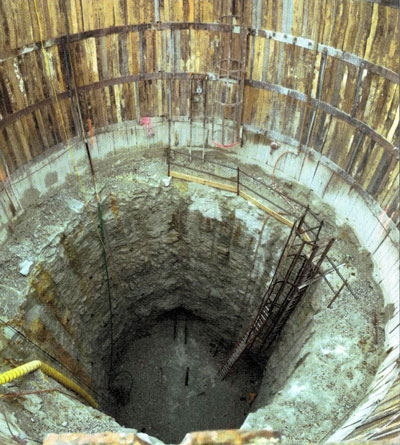